I made this contraption, which I thought would make it easy to crank out clean, true, right angle plank cuts with just a circular saw.
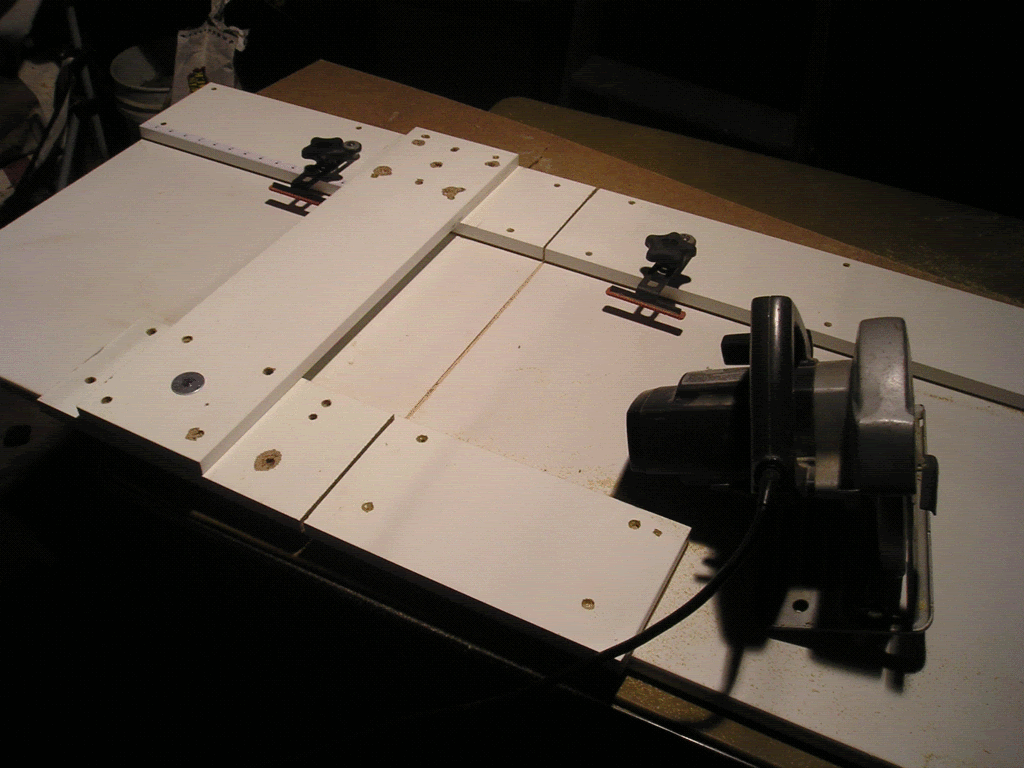
Note: those blown out screw holes are from my first two attempts at securing the guide board and not getting it perfectly square.
Seemed like a good idea but the cuts aren’t turning out as true as I’d like. They’re pretty close, overall 90 degrees, but just wobbly enough to bug me. Everything glides along smoothly when I cut. It seems like it should be working quite nicely…but then I end up with this.
The guide board looks pretty damn true against a straight edge. I don’t know if it’s not as true as it looks, or it’s the play in my cheap circular saw, or if I’m just not as steady as I think am. Any ideas on how to improve this situation?
You could talk me into getting a good circular saw. That's something I actually use. I’m starting to consider forking out for a table saw but my experience is cheap ones are a pain to use and a good one seems like an extravagant expenditure for how much I’ll use it.
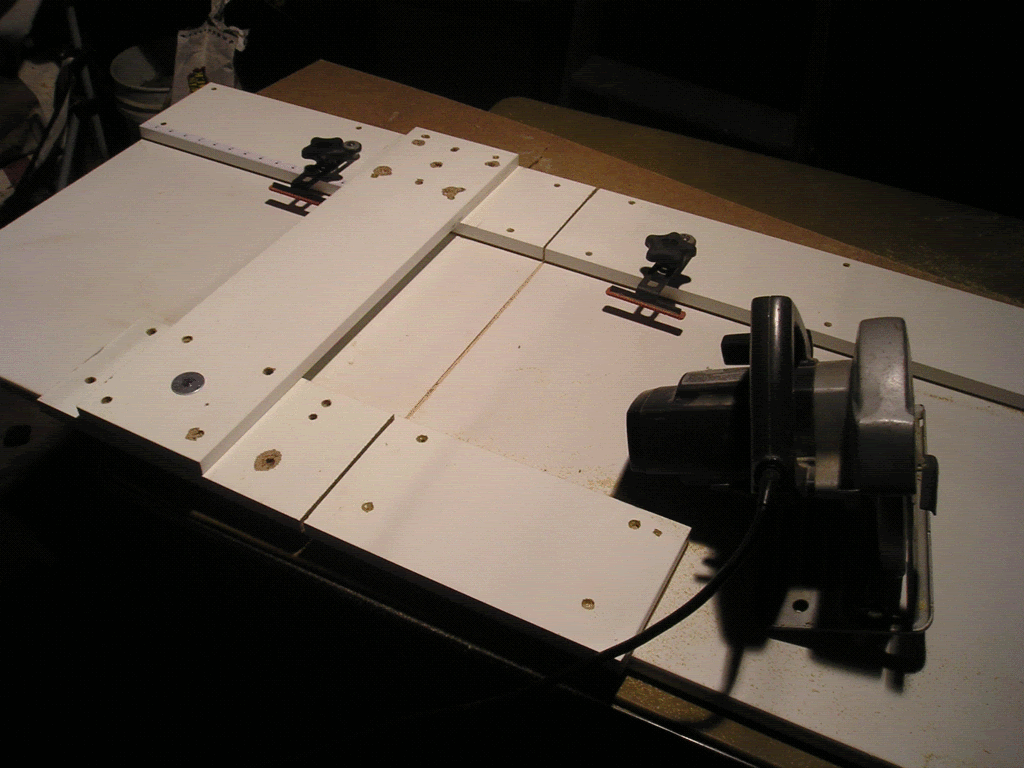
Note: those blown out screw holes are from my first two attempts at securing the guide board and not getting it perfectly square.
Seemed like a good idea but the cuts aren’t turning out as true as I’d like. They’re pretty close, overall 90 degrees, but just wobbly enough to bug me. Everything glides along smoothly when I cut. It seems like it should be working quite nicely…but then I end up with this.
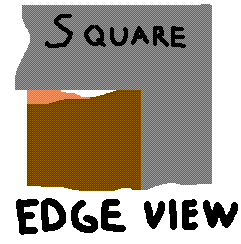
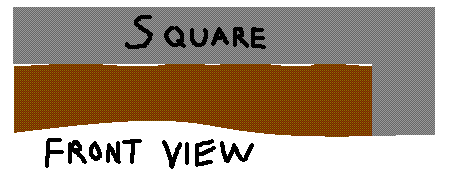
The guide board looks pretty damn true against a straight edge. I don’t know if it’s not as true as it looks, or it’s the play in my cheap circular saw, or if I’m just not as steady as I think am. Any ideas on how to improve this situation?
You could talk me into getting a good circular saw. That's something I actually use. I’m starting to consider forking out for a table saw but my experience is cheap ones are a pain to use and a good one seems like an extravagant expenditure for how much I’ll use it.
Comment