Hello - I'm new to these forums. I was told to come here by one of your members (Jim from jdguitarworks.com) when I reached out to him for a second set of eyes on my winding machine. I asked him because I found that only his one-off machine and one from ukcnc.net were comparable to what I had been developing.
Anyway, I've just been browsing around reading threads here and I feel like this is a good scrutinizing crowd to subject my machine to. You can see a bit about it at www.ac-2.net (this isn't an advertisement, it's not even for sale yet).
Here's a few of the most prominent features:
There's a bunch more I could go on about, like fancy dual core microcontrollers and whatnot, but you get the idea. I suppose that last bullet point sounds like I'd be giving you an incomplete product, but really it's extremely sophisticated and I'm very proud of it. I do know that I want to implement a pickup design sharing repository in the future so users can pass their designs back and forth. I have a couple ideas like this, but I don't feel they should hold up the release of the machine since all of the major stuff is thoroughly checked off already.
I'd like to hear your thoughts, pickup makers and pickup winding machine enthusiasts, on the AC-2 Auto Coil Machine I've just done a poor job describing, as well as what you'd like to see implemented in your ideal pickup winding machine. Also, if you have any questions, I can answer those as well.
I have a fairly old prototype test video on the website up there, but it was done with an early 3D printed prototype and it didn't do a good job of demonstrating the various features...I promise to update that ASAP with the 2.5mm steel chassis version.
Anyway - please let me know if this is something you'd be interested in using, and if not, I'd like to know why. I appreciate constructive criticism!
e: I'll post a few pictures!

A render of the machine - I'll upload real pictures of the steel version as soon as my machinists get their sh...stuff together.


Just a couple more drawings/renders to get a feel for the machine's size - the largest dimension (front across) is 300mm. Pretty tight design! The internal components are well ventilated though, so don't worry - the power supply has its own ventilation port and automatic fan system, as well as being isolated by a steel firewall to prevent excess heat landing on the circuit board. The circuit board's drivers both sit on a large vertical heat sink (keeping the heat off of the board) which is ventilated by a single 80mm fan pulling air out of the cavity. If this proves to be not enough (I'm sure it'll be more than enough really), then there's already a secondary design which utilizes a third fan - a 5v blower fan which rushes the heat right off the driver's heatsink out the back.
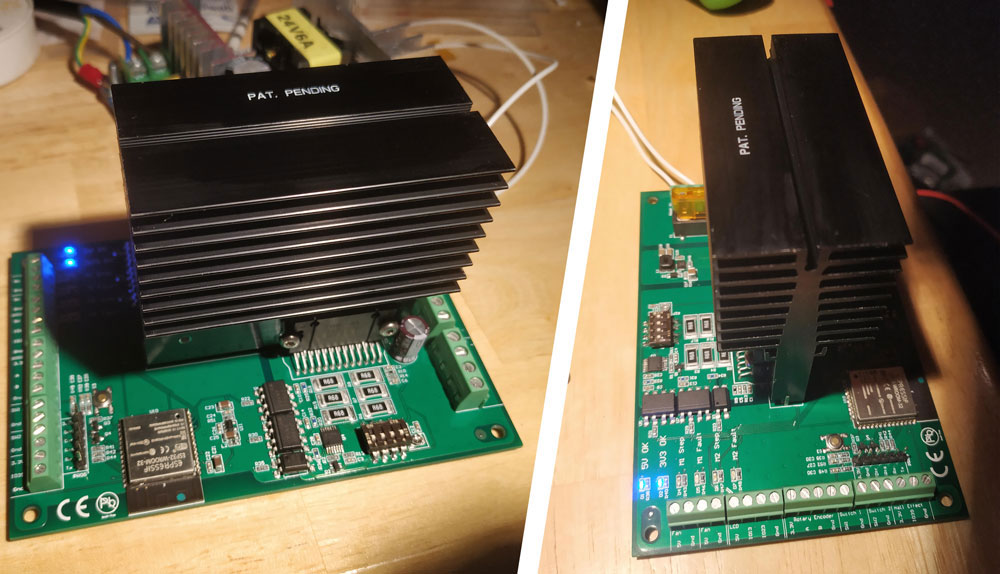
Custom circuit - designed around the Espressif ESP-32 WROOM microcontroller. Very fast, dual core RTOS functionality, wifi connectivity. This machine actually does make use of both cores by operating two state machines simultaneously - one for the GUI, one for the motor functions. This ensures no loss in performance or annoying GUI delays. Everything operates immediately - bug-free too
I'll post some more videos and pictures of the live machine when it's all assembled, I hope you all don't mind waiting a tiny bit for that - it'll be worth it!
Anyway, I've just been browsing around reading threads here and I feel like this is a good scrutinizing crowd to subject my machine to. You can see a bit about it at www.ac-2.net (this isn't an advertisement, it's not even for sale yet).
Here's a few of the most prominent features:
- Auto winding - various modes of operation, including area focus, oscillation mode (winds per sweep) / pattern mode (scatter sim), user-set RPMs, etc
- Manual winding - two main modes: full-manual (2-hand mode), preset manual (1-hand mode - you program the RPMs and # of winds, then just control the wire distribution)
- Polarity sensor - detects pole orientation and also displays magnet field strength.
- 50 save slots (likely to be increased to 100 the moment someone says they need more)
- Built-in compact wire tensioning system utilizing ceramic eyelets and pulleys, a felt disc spring tensioner, and an extremely accurate ruby-tipped wire distribution nozzle.
- A completely original, easy-to-navigate touchscreen GUI that does a great job simplifying a complex process.
- Smart block-based winding pattern creation - users can program and layer up to 20 blocks of different winding parameters within a single pickup design. (the number of blocks is liable to increase if people find need for it)
- Complete system updates via WiFi - connect your machine to your local area network and it will find and install the latest updates for the MCU core functions as well as the entire GUI. This is how I will continue to roll out improvements and new features in the future.
There's a bunch more I could go on about, like fancy dual core microcontrollers and whatnot, but you get the idea. I suppose that last bullet point sounds like I'd be giving you an incomplete product, but really it's extremely sophisticated and I'm very proud of it. I do know that I want to implement a pickup design sharing repository in the future so users can pass their designs back and forth. I have a couple ideas like this, but I don't feel they should hold up the release of the machine since all of the major stuff is thoroughly checked off already.
I'd like to hear your thoughts, pickup makers and pickup winding machine enthusiasts, on the AC-2 Auto Coil Machine I've just done a poor job describing, as well as what you'd like to see implemented in your ideal pickup winding machine. Also, if you have any questions, I can answer those as well.
I have a fairly old prototype test video on the website up there, but it was done with an early 3D printed prototype and it didn't do a good job of demonstrating the various features...I promise to update that ASAP with the 2.5mm steel chassis version.
Anyway - please let me know if this is something you'd be interested in using, and if not, I'd like to know why. I appreciate constructive criticism!
e: I'll post a few pictures!

A render of the machine - I'll upload real pictures of the steel version as soon as my machinists get their sh...stuff together.


Just a couple more drawings/renders to get a feel for the machine's size - the largest dimension (front across) is 300mm. Pretty tight design! The internal components are well ventilated though, so don't worry - the power supply has its own ventilation port and automatic fan system, as well as being isolated by a steel firewall to prevent excess heat landing on the circuit board. The circuit board's drivers both sit on a large vertical heat sink (keeping the heat off of the board) which is ventilated by a single 80mm fan pulling air out of the cavity. If this proves to be not enough (I'm sure it'll be more than enough really), then there's already a secondary design which utilizes a third fan - a 5v blower fan which rushes the heat right off the driver's heatsink out the back.
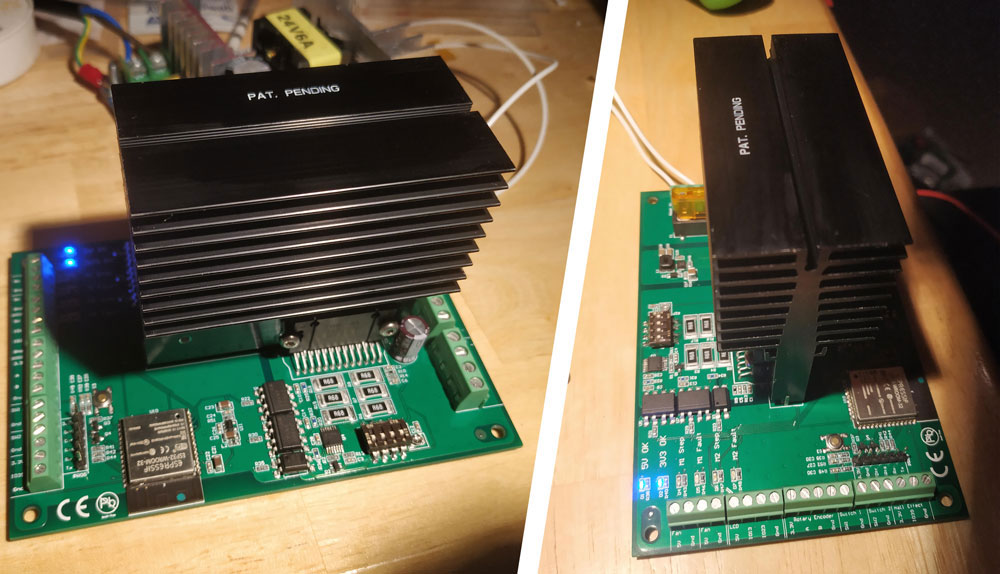
Custom circuit - designed around the Espressif ESP-32 WROOM microcontroller. Very fast, dual core RTOS functionality, wifi connectivity. This machine actually does make use of both cores by operating two state machines simultaneously - one for the GUI, one for the motor functions. This ensures no loss in performance or annoying GUI delays. Everything operates immediately - bug-free too

I'll post some more videos and pictures of the live machine when it's all assembled, I hope you all don't mind waiting a tiny bit for that - it'll be worth it!
Comment